How CNC Precision Machining Is Revolutionizing Modern Machine Parts Manufacturing
In the world of manufacturing, the pursuit of precision, efficiency, and scalability is unrelenting. Among the transformative technologies redefining this landscape, CNC Precision Machining stands out as a pivotal driver.
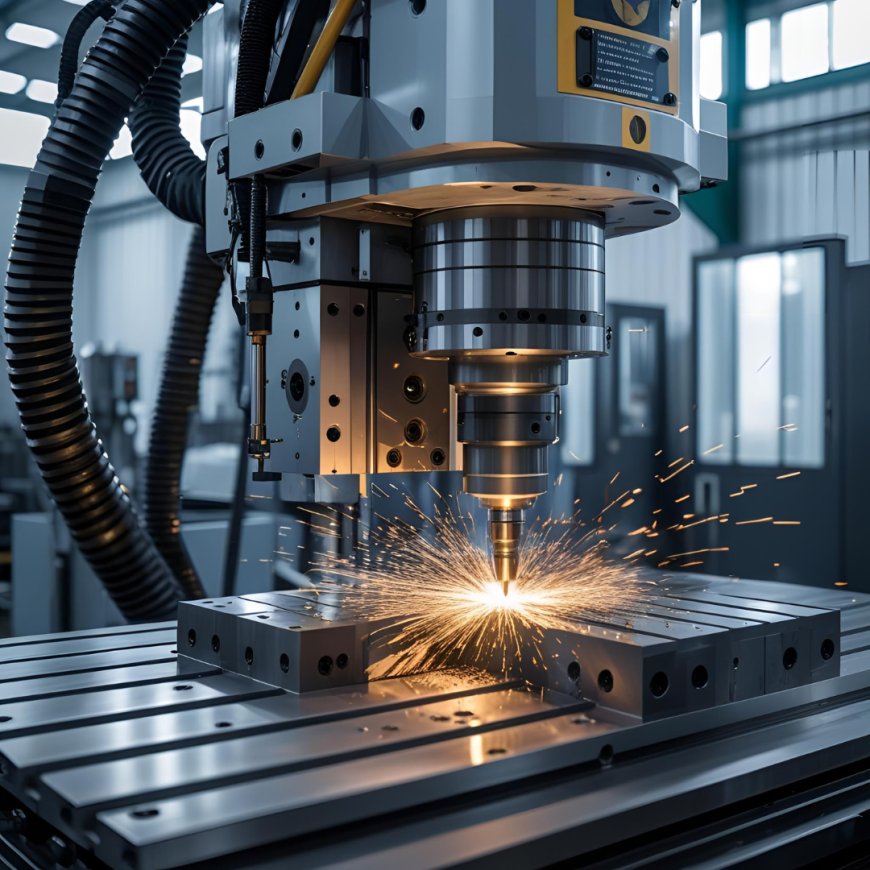
Introduction
In the world of manufacturing, the pursuit of precision, efficiency, and scalability is unrelenting. Among the transformative technologies redefining this landscape, CNC Precision Machining stands out as a pivotal driver. Especially in the realm of machine parts manufacturing, CNC (Computer Numerical Control) machining delivers unmatched accuracy, repeatability, and cost efficiency that traditional techniques struggle to rival. As global industries demand tighter tolerances and more complex geometries, CNC precision machining is fast becoming the cornerstone of competitive production.
Manufacturers that adopt this technology can not only meet rigorous industry standards but also gain an edge through faster prototyping, leaner production, and superior product integrity. In this article, we explore how CNC precision machining is shaping the future of machine parts manufacturing — from its technical foundations to real-world applications.
What Is CNC Precision Machining?
CNC precision machining refers to the process where pre-programmed computer software directs the movement of machinery and tools. These systems can carry out a wide range of complex tasks — including drilling, milling, turning, and grinding — with micrometer-level precision. CNC machining has evolved to accommodate a variety of materials, including metals, plastics, and composites, making it a versatile choice across sectors.
Key Features:
-
Automation: CNC systems reduce human error and labor costs.
-
Accuracy: Modern machines can produce parts with tolerances as tight as ±0.0001 inches.
-
Repeatability: Once a design is programmed, it can be replicated hundreds or thousands of times without variation.
-
Flexibility: From a single prototype to mass production, CNC adapts easily to different batch sizes.
Importance of CNC in Machine Parts Manufacturing
Machine parts demand exceptional durability, uniformity, and dimensional accuracy — attributes that CNC machining delivers consistently. Whether it’s aerospace components, medical implants, or automotive gears, CNC machining ensures that each part functions perfectly within its intended assembly.
Advantages:
-
Complex Geometries: CNC systems handle intricate designs that manual machining cannot achieve.
-
Material Efficiency: Precision cutting reduces waste and lowers material costs.
-
Speed to Market: Faster turnaround from design to final product enhances competitiveness.
-
Quality Assurance: Integrated metrology and inspection processes maintain strict quality standards.
CNC Techniques Used in Machine Parts Production
Several CNC machining techniques are utilized based on the complexity and specifications of the parts:
-
Milling: Rotating cutting tools remove material from a stationary workpiece. Ideal for custom shapes and flat surfaces.
-
Turning: The workpiece rotates while a single-point tool shapes it. Common in shaft and cylinder manufacturing.
-
EDM (Electrical Discharge Machining): Used for hard metals or intricate cavities.
-
Grinding: Produces ultra-smooth finishes and ultra-tight tolerances.
Materials Commonly Used
Machine parts can vary significantly in function and form, necessitating diverse material choices. CNC machines handle:
Material Type |
Common Applications |
Aluminum |
Lightweight frames, housings |
Steel |
Gears, shafts, engine blocks |
Titanium |
Aerospace, medical devices |
Plastics |
Insulators, lightweight components |
Quality Control in CNC Machining
Quality control is embedded at every stage of CNC machining. From the moment raw material enters the shop to the final inspection of the finished component, precision and reliability are paramount. Techniques include:
-
Coordinate Measuring Machines (CMMs): Measure the physical geometrical characteristics of an object.
-
Laser Scanning: For high-speed, non-contact inspection.
-
In-process Monitoring: Real-time tracking of machining conditions for optimal outcomes.
Industry Applications
CNC precision machining is ubiquitous across many sectors due to its adaptability and precision.
-
Aerospace: High-stress components like turbine blades and actuators.
-
Automotive: Gearboxes, pistons, and steering components.
-
Medical: Surgical instruments and orthopedic implants.
-
Electronics: Heat sinks, housings, and connectors.
-
Oil & Gas: Valve bodies, flanges, and downhole tools.
Trends and Innovations
Technological advancements continue to enhance CNC machining capabilities:
-
Multi-Axis Machining: Enables production of complex parts in a single setup.
-
Hybrid CNC Machines: Combine additive and subtractive processes.
-
AI Integration: Predictive maintenance and adaptive process control.
-
Cloud-Based CNC Software: Enables remote programming and real-time monitoring.
Challenges and Mitigations
Despite its strengths, CNC machining faces challenges like:
-
High Initial Costs: Mitigated through long-term savings and improved ROI.
-
Skilled Labor Shortage: Addressed through training programs and digital apprenticeships.
-
Maintenance Needs: Preventive maintenance and monitoring tools reduce downtime.
Conclusion
CNC precision machining is not just a technological upgrade — it’s a manufacturing imperative. For companies focused on machine parts production, embracing this method means enhanced performance, lower defect rates, and a competitive advantage in a demanding global market. As the technology evolves, its influence will only deepen, reshaping how machine parts are designed, manufactured, and deployed across industries.
Staying ahead means not only adopting CNC but optimizing it within your production ecosystem. As the saying goes, the future belongs to those who build it — with precision.
Author’s Note: This article is based on industry best practices and current market data. For custom solutions or CNC manufacturing services, always consult qualified professionals or certified manufacturers.