What Makes a Warehouse Design Practical and Durable
A well-planned warehouse design boosts efficiency, storage, and safety. Discover what makes a warehouse practical, durable, and suitable for long-term industrial use.
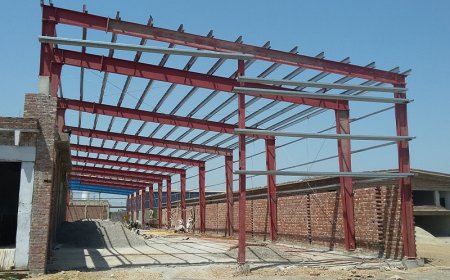
When you're thinking about putting up a new warehouse, it's easy to get caught up in just the basics: how big does it need to be, and how quickly can it go up? But truly effective warehouse design is about so much more than just size and speed. It’s about creating a space that works efficiently for years, handles everything you throw at it, and contributes positively to your operations. A well-thought-out design, combined with solid industrial warehouse construction, makes all the difference in the world.
A warehouse isn't just a big empty box. It's a dynamic hub where goods are received, stored, sorted, and shipped. Every decision made during the design phase has a ripple effect on everything that happens inside those walls, from the movement of forklifts to the safety of your team and the integrity of your products. Skimping on planning or construction quality can lead to bottlenecks, higher operating costs, and even safety hazards down the line. Let's explore what truly makes a warehouse practical and durable.
Understanding Your Operational Flow
Before any design sketches are even made, the most important step is to deeply understand what activities will take place inside the warehouse. This is often called understanding your operational flow.
Receiving and Shipping Zones
How will goods arrive and depart? Do you need multiple loading docks for different types of vehicles? What’s the expected volume of incoming and outgoing shipments? Designing dedicated, spacious, and easily accessible areas for receiving and shipping minimizes congestion, speeds up turnaround times, and reduces the risk of accidents. Think about the path trucks will take, where they’ll park, and how efficiently goods can move from the truck into storage, or from storage onto the truck.
Storage Needs and Material Handling
What kind of items will you store? Are they palletized, bulky, temperature-sensitive, or hazardous? This will dictate the type of shelving, racking, and material handling equipment you'll need. The design should account for the clear height required for your highest racks, the aisle widths needed for forklifts to maneuver safely, and any specialized storage requirements like cold rooms or secured cages. A layout that supports smooth material handling pathways helps avoid bottlenecks and improves productivity.
Picking and Packing Areas
For many operations, the picking and packing zones are crucial. These areas need to be ergonomically designed, well-lit, and close to the relevant storage areas. The layout should facilitate an easy flow from picking to packing to dispatch, minimizing unnecessary movement and reducing errors.
Structural Integrity and Durability
The physical building itself needs to be robust. This goes beyond just looking strong; it means the materials and construction methods are chosen for long-term performance.
Foundation Matters
Just like any building, a warehouse’s foundation is everything. It needs to be engineered to support heavy loads from racking, machinery, and stored goods, as well as resist any ground movement. The type of soil, the climate, and the expected loads all influence the foundation design. A strong, stable foundation prevents future issues like cracking floors or structural settling.
Robust Framing and Walls
The structural frame – whether it's steel, pre-engineered metal, or concrete – must be capable of bearing the immense loads of the roof, any suspended equipment, and environmental forces like wind and snow. The walls need to be durable enough to withstand daily bumps from forklifts and pallets, and provide adequate insulation for temperature control. Materials that are easy to clean and maintain also contribute to the overall durability and longevity of the structure.
Flooring Designed for Heavy Use
Warehouse floors take a beating. They must be incredibly strong, flat, and resistant to abrasion from forklifts, spills, and heavy foot traffic. The right concrete mix, proper curing, and sometimes specialized coatings are essential to prevent cracking, dusting, and premature wear. A well-designed floor reduces maintenance, improves safety, and allows for smoother operation of material handling equipment.
Environmental Control and Sustainability
A practical warehouse isn't just about space; it's about creating the right internal environment for your products and your people.
Ventilation and Air Quality
Proper ventilation is crucial, especially in warehouses where dust, fumes, or temperature extremes might be an issue. A good system ensures fresh air circulation, removes stale air, and helps manage temperature and humidity. This protects both your goods and your workforce. Natural ventilation can be effective in some climates, but mechanical systems offer more precise control, which is often necessary for sensitive products or large spaces.
Temperature and Humidity Management
For many products, maintaining a specific temperature and humidity range is vital. This requires careful consideration of insulation, roofing materials, and HVAC systems. A well-insulated building reduces energy consumption for heating and cooling, leading to lower operating costs over the building's lifespan. Some companies, such as Shelter Engineering, focus on delivering durable construction for industrial spaces, understanding the importance of these environmental controls in their projects. Their work on various warehouse projects, which you can explore at: https://sheltersengineering.com/warehouse-construction-company-pakistan/
shows a commitment to practical and long-lasting solutions.
Lighting Solutions
Adequate lighting is essential for safety, accuracy in picking, and overall productivity. A mix of natural light (where possible, through skylights or windows designed to minimize heat gain) and efficient artificial lighting (like LED fixtures) is ideal. Good lighting reduces eye strain for workers and helps prevent errors.
Safety and Security Features
A durable warehouse is a safe warehouse. Integrating safety and security features from the initial design phase is paramount.
Fire Safety Systems
Fire detection and suppression systems are non-negotiable. This includes strategically placed sprinklers, fire alarms, clearly marked emergency exits, and fire-resistant materials in key areas. The layout should also allow for easy access for emergency services.
Egress and Emergency Exits
Clear, unobstructed emergency exits are vital for the safety of everyone in the building. These must be well-marked and easily accessible from all parts of the warehouse, and the design should ensure that pathways to these exits are always clear.
Security Measures
Think about how to prevent unauthorized access. This includes robust perimeter fencing, secure entry points, surveillance camera placement, and lighting around the exterior. The design can also incorporate features that make it difficult for intruders to bypass security.
Expandability and Flexibility
The business world changes rapidly, and your warehouse should be able to change with it. A truly practical design considers future growth and evolving needs.
Modular Design Principles
Designing the warehouse with a modular approach allows for easier expansion later on. This might involve planning for future wall removals, or ensuring that utilities and infrastructure can be extended without major overhauls.
Adaptable Layouts
Can your internal layout be easily reconfigured if your storage needs change or if you introduce new material handling equipment? Column spacing, ceiling height, and utility access points should be considered with future flexibility in mind. A design that can adapt to different racking systems or automation technologies will save you significant money and downtime if your operational needs shift.
The Long-Term Value of Good Design and Construction
Ultimately, what makes a warehouse design practical and durable isn't just one thing, but a combination of thoughtful planning, robust materials, and expert execution. Investing in high-quality industrial warehouse construction from the outset prevents costly repairs, improves operational efficiency, boosts safety, and gives you a facility that truly supports your business goals for decades to come. It’s an investment that keeps paying off, ensuring your operations run smoothly and effectively, regardless of what the future holds.