Learn How to Develop Effective PPE Safety Procedures
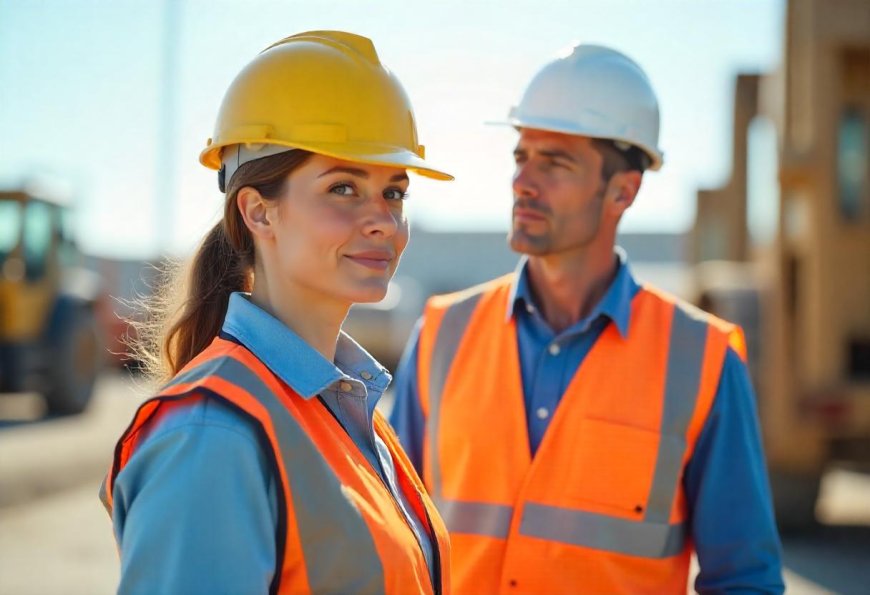
When you step into a workplace — whether it’s a construction site, a chemical plant, or even a busy warehouse — you’ll see workers wearing gloves, hard hats, boots, and goggles. All these items are called Personal Protective Equipment (PPE), and they serve as the last line of defense against injuries. But having PPE is not enough. You must know how to develop proper PPE safety procedures to make sure that this equipment really protects people.
It’s shocking, but true: every year, thousands of workers get injured or even die because they didn’t use their PPE correctly, or their workplace didn’t have proper procedures in place. That’s why developing a solid plan is so important. If you work in safety or manage a team, or even if you are a worker yourself, you need to understand how to build a reliable PPE system.
Interestingly, safety experts and those who take professional safety courses like a NEBOSH Course in Multan often become champions of PPE practices. These programs teach in-depth hazard management, which supports the skills you’ll read about today. Let’s break down, step by step, how you can develop PPE safety procedures that genuinely save lives.
Why PPE Safety Procedures Matter
Imagine a worker on a welding site. He’s wearing a helmet, but it’s not properly adjusted. Sparks fly, and the helmet shifts, exposing his face. That’s a painful injury that could have been avoided with the correct procedure.
PPE is not a magical shield — it only works if people know exactly when, how, and why to use it. Without proper safety procedures, equipment can fail, leaving workers exposed to serious workplace hazards.
PPE programs protect not only the workers but also the company’s reputation and finances. After all, injury claims, lost work hours, and legal battles are far more expensive than investing in proper protective procedures.
Step 1: Identify Workplace Hazards
Before you even buy PPE, you need to know what hazards exist. This is where a proper hazard assessment comes into play. Walk through your worksite, observe tasks, and talk to workers. Look for dangers like:
-
Chemical exposures (fumes, acids, solvents)
-
Physical hazards (falling objects, sharp tools, noise)
-
Biological threats (viruses, bacteria)
-
Ergonomic risks (awkward lifting, repetitive tasks)
When you clearly identify these hazards, you can choose the right PPE for each risk.
Pro Tip: Think of this step like checking the weather before you travel — you wouldn’t pack your bags without knowing what to expect, right?
Step 2: Select the Right PPE
Once you know the hazards, match them with the proper PPE. For example:
-
Chemicals → gloves, goggles, chemical-resistant aprons
-
Falling objects → hard hats, steel-toe boots
-
Noise → earplugs or earmuffs
-
Sparks or heat → flame-resistant clothing, face shields
One size does not fit all. In fact, the wrong PPE can be more dangerous than no PPE at all, because it gives a false sense of security. Always check PPE certifications and standards before purchasing.
If you’re unsure, ask a safety expert, or consult guidelines taught in training programs similar to the NEBOSH IGC Course in Multan to confirm what’s best for your workplace.
Step 3: Develop a PPE Policy
After you select the gear, you need rules for using it. A PPE policy should cover:
-
When to wear PPE
-
How to inspect and maintain it
-
Where PPE should be stored
-
What to do if PPE is damaged or missing
-
Disciplinary steps for failing to comply
A clear policy helps avoid confusion. Workers can’t follow procedures they don’t know about.
Anecdote: I once met a site supervisor who thought everyone would “just know” when to wear gloves. Unfortunately, a new worker didn’t know, suffered a serious cut, and the company was held responsible. A simple policy could have prevented that.
Step 4: Train Your Team
Even the best equipment fails if workers don’t know how to use it. PPE training should include:
-
How to properly wear and adjust PPE
-
When to replace or discard damaged PPE
-
How to clean or sanitize PPE
-
How PPE fits with other safety procedures
Use real-life demos. Let workers practice. And don’t just train them once — repeat it regularly.
Transition words like meanwhile, additionally, and in other words can help your trainers explain complicated ideas in simpler terms.
Step 5: Supervise and Enforce
Sadly, some workers will ignore PPE rules if no one checks. Supervision is essential. Supervisors should monitor compliance every day. If a worker refuses to follow the PPE rules, take corrective action immediately.
But try to encourage rather than punish. Make PPE part of the workplace culture by explaining how it protects families, not just workers. After all, nobody wants to bring an injury home to their loved ones.
Step 6: Inspect and Maintain PPE
PPE is like a car: it needs regular checkups. Build inspection routines into your schedule:
-
Check for cracks in helmets
-
Inspect gloves for holes
-
Test respirators for leaks
-
Replace damaged eye protection
Encourage workers to report worn-out PPE without fear of getting blamed. You want them to speak up so they can stay safe.
Step 7: Review and Improve
Workplaces change over time. New machines, new chemicals, or even a simple change in layout can introduce new risks. You should review your PPE program at least once a year, or after any major change or accident.
Ask for feedback from workers. They are the ones on the front line. Their insights will help you refine and improve your procedures.
Real-World Example of Poor PPE Procedures
Let’s talk about a friend of mine who worked in a paint factory. They had masks available but no training on how to wear them. Workers wore them loosely, thinking they were enough to block paint fumes. Over time, many developed breathing problems.
Eventually, the factory invested in proper PPE training and strict supervision, and incidents dropped dramatically.
That story shows how effective PPE procedures can transform a workplace from dangerous to safe.
Integrating PPE with Other Safety Systems
PPE is only one piece of the puzzle. You should connect it with other systems, like:
-
Safety signage
-
Safe work procedures
-
Emergency response plans
-
Equipment maintenance
For example, if you work with flammable liquids, your PPE should match your fire safety plan. Everything should work together, like gears in a well-oiled machine.
Overcoming Resistance to PPE Rules
Let’s be honest: some people think PPE is uncomfortable or unnecessary. How do you change their mindset?
-
Share real injury stories (without scaring them, but being truthful)
-
Remind them about their families who depend on them
-
Involve workers in choosing comfortable PPE
-
Offer incentives for consistent compliance
By treating workers as partners instead of just “rule followers,” you build a positive PPE culture.
The Financial Benefits of Strong PPE Programs
Besides saving lives, effective PPE safety programs save money. Fewer injuries mean:
-
Lower insurance costs
-
Less time lost
-
Higher morale
-
Better company reputation
Think of PPE as an investment, not an expense. A single serious accident could cost your business more than an entire year’s worth of PPE costs.
Read more about how NEBOSH IGC Course in Multan can help you boost your safety career.
Wrapping Up: Why You Should Start Now
Developing PPE safety procedures is not just a paperwork exercise. It’s a lifeline for workers. From hazard assessments to training, every step builds a protective wall around your team. Remember:
-
PPE is your last defense
-
Policies keep everyone on the same page
-
Training makes PPE usable
-
Regular inspections keep PPE working
-
Reviews help you stay current
If you put in the effort to build a solid PPE program, you’ll help ensure everyone gets home safely at the end of the day. And that, truly, is priceless.