How to choose the right boiler tube cleaner machine for your facility
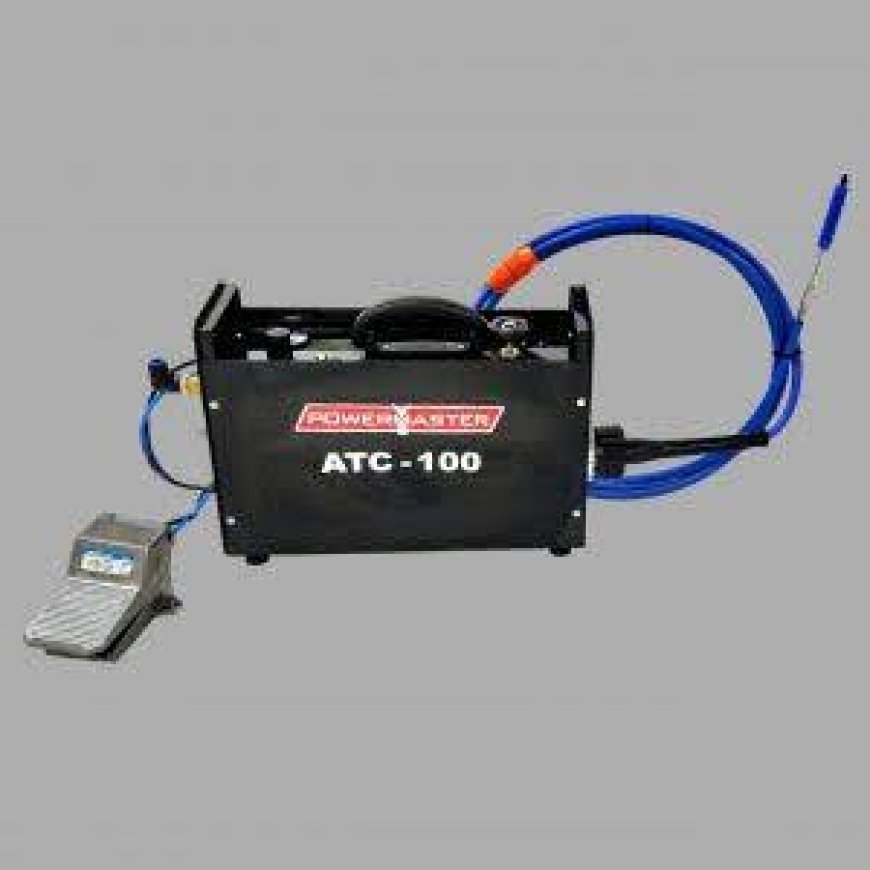
Introduction
The choice of the right boiler tube cleaner machine guarantees the best maintenance and operational effectiveness in any facility. An appropriate unit will eliminate as much downtime as possible and prolong the life of the equipment by ensuring effective removal of deposits and scale. Decision makers are compelled to incorporate trade-offs between cleaning performance and practicality to fit particular boiler set ups. A logical assessment of the main factors directs to a trusted and cost-effective decision in the end.
Assess facility requirements
The operational parameters of the facility should be carefully evaluated before choosing a boiler tube cleaner machine. These factors are the size of the boiler, the diameter of the tubes, configuration, and availability of cleaning devices. Assessment of deposits type (soot, scale or corrosion products) informs selection of cleaning technique and abrasive. Also, facility managers must keep in mind the frequency of cleaning, the runtime availability, and compatibility with existing maintenance plans. The selected system meets these requirements and provides effective cleaning performance, less downtime, and sustainable boiler efficiency in the long term due to a matching of the machine specification to the real-world operational requirements.
Evaluate cleaning mechanisms
Various boiler tube cleaner machines use different cleaning methods, including high-pressure water jets, rotary brushes, and pneumatic impact tools. The advantages of each technology are distinct: water jets are able to remove mineral and soot deposits effectively without any risk to tube wall integrity, whereas rotary brushes can tackle the most stubborn deposits with aggressive mechanical cleaning action. Pneumatic impact tools remove scale via regulated hammering. The knowledge of the trade-offs among cleaning speed, surface integrity, and maintenance requirements can assist decision makers in choosing a method that best balances efficacy, tube protection and long-term reliability relative to the needs of their particular facility.
Consider portability and power source
The suitability of a tube cleaner machine is highly dependent on its mobility and power options. Electrically driven portable devices provide reliable operation in facilities where power infrastructure is reliable, whereas pneumatically powered machines provide flexibility in facilities where a consistent source of compressed air is available but where electrical power is not reliably available. The weight, transportation, and set-up time must be compared to operational priorities to guarantee quick deployment. In addition, it is possible to choose machines that have variable power settings so technicians can adjust to lower energy and equipment wear without compromising on complete removal of fouling materials.
Review maintenance and safety features
Sustained operation and compliance require maintenance needs and safety features. With easily reachable wear parts, quick change nozzles, and easy inspections, machines are easier to service often and keep unexpected downtime to a minimum. For high-pressure cleaning, safety interlock and pressure relief valves or automatic shutoff are used to safeguard the operator against exposure to a hazard. Also, ergonomic features in the equipment, like adjustable handles and sound less features, make the operators more comfortable and productive. Finding a balance between machines that are easy to maintain and machines with all-round safety measures helps maintain the level of cleaning, safety compliance with the rules, and costs.
Budget and additional functionality
Budget considerations are bound to influence the selection process; however, cost should not be chosen over performance and longevity. Comparisons of the initial capital expense to total ownership costs, such as the cost of maintenance, energy costs, and replacement parts should be made by the evaluators. Robots that provide modular accessories, such as specialized nozzles or reversible cleaning heads, are versatile to accommodate different types of deposits and tube shapes. Users who want to have integrated controls or data logging abilities are able to optimize cleaning schedules and equipment performances. The balance between initial investment cost and sensible improvements, facilities find themselves with a strong long-lasting pipe tube cleaner solution that performs consistently.
Conclusion
Selection of a correct boiler tube cleaner machine can be done by analyzing specifications, cleaning procedures, power requirements, maintenance requirements and budget. This organized method ensures effective deposit clean up, lower idle time and improved equipment life. With features highlighting practical performance and safety, teams can feel secure investing in a solution that ensures dependable boiler operation and can result in cost savings over the long-term approach.